All you need to know about CO2 incubator(2)
What is a CO2 incubator?
A carbon dioxide incubator is a device for in vitro cultivation of cells/tissues by simulating the formation of a growth environment similar to that of cells/tissues in a living organism inside an incubator chamber, which requires a stable temperature (37°C), a stable level of CO2 (5%), a constant acidity/alkalinity (pH:7.2-7.4), and a high relative saturated humidity (95%).
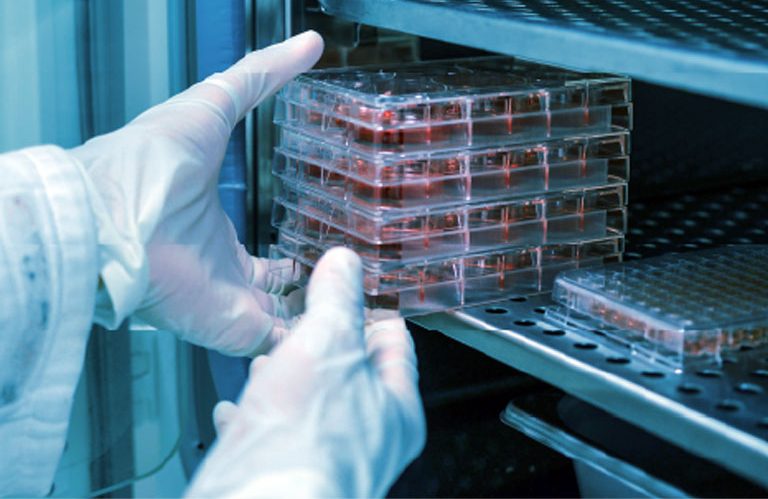
Carbon dioxide concentration control for CO2 incubator.
Carbon dioxide concentration can be measured by either an infrared sensor (IR) or a thermo conductive sensor (TC). Both sensors have their advantages and disadvantages.
Thermal Conductivity Sensor for CO2 incubator.
The principle of operation of the thermal conductivity sensor for monitoring CO2 concentration is based on the continuous measurement of the thermal conductivity of the air in the chamber. The low thermal conductivity of the input CO2 gas causes a change in the thermal conductivity of the air in the chamber, which generates an electrical signal directly proportional to the CO2 concentration.
A disadvantage of the TC control system is that changes in temperature and relative humidity inside the chamber can affect the accuracy of the sensor. When the chamber door is opened frequently, not only the CO2 concentration, but also the temperature and relative humidity fluctuate greatly, thus affecting the accuracy of the TC sensor. This control system is not suitable when precise incubation conditions are required and the incubator door is opened frequently.
Infrared Sensor for CO2 incubator.
The Infrared Sensor (IR) detects the CO2 level by means of an optical sensor.The IR system consists of an infrared emitter and a sensor.When the CO2 in the chamber absorbs part of the infrared light emitted by the emitter, the sensor detects a reduction in the infrared light, and the amount of infrared light absorbed corresponds to the level of CO2 in the chamber, which results in the CO2 concentration in the chamber. concentration in the box. Because the IR system is through the infrared reduction to determine the concentration of CO2 in the box, and the particles in the box can reflect or partially absorb infrared rays, so that the IR system is more sensitive to the amount of particles in the box, the IR sensor is more appropriate to be used in the air intake with a HEPA high-efficiency air filters in the incubator.
Relative humidity for CO2 incubator.
Humidity in the incubator is a very important but often overlooked factor for culture work. Maintaining a sufficient humidity level and a fast enough humidity recovery (e.g. after opening and closing the door) ensures that the culture does not fail due to over-drying.
Most current CO2 incubators produce humidity by evaporation from a humidifier tray (which produces relative humidity levels up to about 95%, but humidity recovery is slow after the door is opened and closed). Try to choose an incubator with a large humidity evaporation area, because the larger the humidity evaporation area, the easier it is to reach the maximum relative saturation humidity and the shorter the humidity recovery time after opening and closing the door.
Control of Contaminants for CO2 incubator.
Contamination is a major factor in cell culture failure. Manufacturers of CO2 incubators have designed a number of different devices to reduce and prevent contamination from occurring, the main way is to minimize the areas and surfaces on which microorganisms can grow, and combined with automatic decontamination devices to effectively prevent contamination from occurring.
A carbon dioxide incubator is a device for in vitro cultivation of cells/tissues by simulating the formation of a growth environment similar to that of cells/tissues in a living organism inside an incubator chamber, which requires a stable temperature (37°C), a stable level of CO2 (5%), a constant acidity/alkalinity (pH:7.2-7.4), and a high relative saturated humidity (95%).
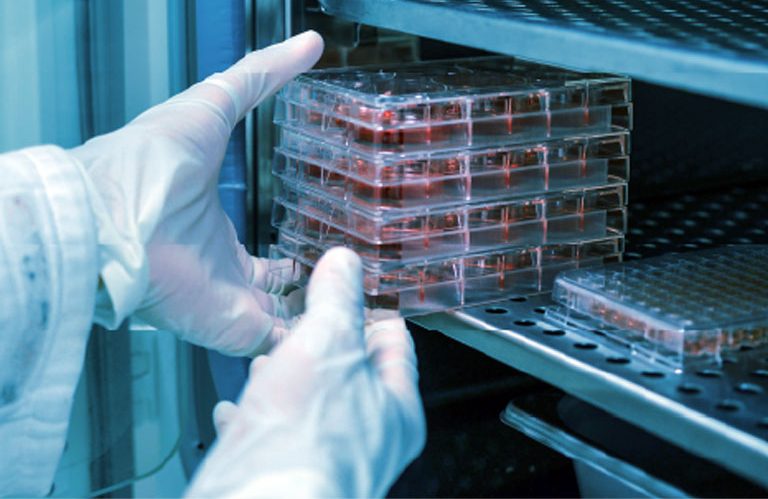
Carbon dioxide concentration control for CO2 incubator.
Carbon dioxide concentration can be measured by either an infrared sensor (IR) or a thermo conductive sensor (TC). Both sensors have their advantages and disadvantages.
Thermal Conductivity Sensor for CO2 incubator.
The principle of operation of the thermal conductivity sensor for monitoring CO2 concentration is based on the continuous measurement of the thermal conductivity of the air in the chamber. The low thermal conductivity of the input CO2 gas causes a change in the thermal conductivity of the air in the chamber, which generates an electrical signal directly proportional to the CO2 concentration.
A disadvantage of the TC control system is that changes in temperature and relative humidity inside the chamber can affect the accuracy of the sensor. When the chamber door is opened frequently, not only the CO2 concentration, but also the temperature and relative humidity fluctuate greatly, thus affecting the accuracy of the TC sensor. This control system is not suitable when precise incubation conditions are required and the incubator door is opened frequently.
Infrared Sensor for CO2 incubator.
The Infrared Sensor (IR) detects the CO2 level by means of an optical sensor.The IR system consists of an infrared emitter and a sensor.When the CO2 in the chamber absorbs part of the infrared light emitted by the emitter, the sensor detects a reduction in the infrared light, and the amount of infrared light absorbed corresponds to the level of CO2 in the chamber, which results in the CO2 concentration in the chamber. concentration in the box. Because the IR system is through the infrared reduction to determine the concentration of CO2 in the box, and the particles in the box can reflect or partially absorb infrared rays, so that the IR system is more sensitive to the amount of particles in the box, the IR sensor is more appropriate to be used in the air intake with a HEPA high-efficiency air filters in the incubator.
Relative humidity for CO2 incubator.
Humidity in the incubator is a very important but often overlooked factor for culture work. Maintaining a sufficient humidity level and a fast enough humidity recovery (e.g. after opening and closing the door) ensures that the culture does not fail due to over-drying.
Most current CO2 incubators produce humidity by evaporation from a humidifier tray (which produces relative humidity levels up to about 95%, but humidity recovery is slow after the door is opened and closed). Try to choose an incubator with a large humidity evaporation area, because the larger the humidity evaporation area, the easier it is to reach the maximum relative saturation humidity and the shorter the humidity recovery time after opening and closing the door.
Control of Contaminants for CO2 incubator.
Contamination is a major factor in cell culture failure. Manufacturers of CO2 incubators have designed a number of different devices to reduce and prevent contamination from occurring, the main way is to minimize the areas and surfaces on which microorganisms can grow, and combined with automatic decontamination devices to effectively prevent contamination from occurring.